Training supports understanding to help pigs and employees reach their potential.
Employment needs in the swine industry grew nearly four times faster in the last 20 years than employment growth in all other industries.[1] So, how can U.S. pork producers compete with other employers and retain talented employees to provide excellent, efficient animal care?
“In my experience, employees with access to training and training resources are better prepared to do great work and are more motivated,” says Stacey Voight, Pig Improvement Company (PIC) Reproduction Technical Services. “When employees are well trained and engaged in their roles, they can complete all necessary tasks and provide sows and pigs with the best possible care to reach their full potential.”
Voight, along with Neal Paszkiewicz, head of training and development with Wakefield Pork, and Ashely Hengen, PIC Senior Human Resources Generalist, shares insights about the benefits of training they’ve observed and resources that can be used to supplement current farm training programs.
What are the current challenges to providing training?
Paszkiewicz: The experience level of the individuals we bring in today is completely different from that in the past. As employers and managers, we must remember that things we take for granted are new to others. It’s becoming more and more important to have a conversation to put new employees at ease and get a sense of what they might be interested in.
Voight: Finding the time to train is the biggest constraint for today’s farms. Another challenge is providing information in a way the employee will be able to understand and remember. PIC has focused on delivering technical information in multiple training formats so farm employees can find a format that works well for them.
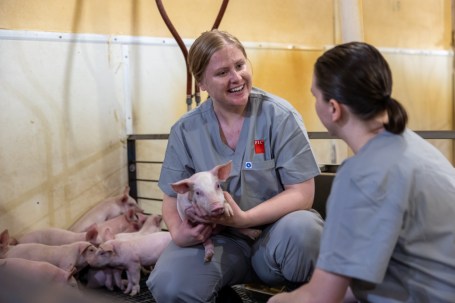
How can training pay off for an operation?
Voight: Training for new and current employees supports better animal welfare, animal performance and farm profitability. For example, PIC has created several calculators to help demonstrate the value of a 1% change in a variety of key performance indicators so employees can visibly see the value of their influence. These small improvements can add up over time to create significant value. For example:
- On a 3,600-sow farm with an average of 16 pigs born per litter and a $35/piglet price, a 1% difference in pigs converted per year delivers $48,384 in value.
- On a 5,000-sow farm with 90% gilt utilization and a gilt cost of $300, the value of a 1% change in sow survivability per year is $27,467.
- On a 5,000-head farrow-to-finish operation achieving 25 pigs per sow per year, improving grow-finish survivability by 1% between 11 and 14 weeks post-weaning would support $125,000 savings annually. (Assumes feed cost of about $0.11 per pound and a market price of about $80 per cwt.)
What’s one new training strategy you’ve seen that boosts employee confidence and, ultimately, farm productivity?
Voight: The use of training videos to demonstrate concepts has been very successful. I often recommend to managers I work with to have new employees watch training videos and review training materials before they get to the farm. For example, if the new team member will be working in farrowing, they can watch instructional videos for that area before seeing it firsthand. This will help them retain information about animal care before working with the animals. This approach is also beneficial to help employees prepare for changes in management strategies or farm protocols.
Hengen: Training employees to do multiple tasks is a tactic that has worked well on PIC-owned farms. The team strives to give employees a chance to try the many tasks that need to get done every day rather than assigning employees to only one task. This allows them to try a variety of hands-on production tasks and understand how all tasks fit together.
Paszkiewicz: It is important for employees to learn a variety of tasks and to meet different people throughout an operation. Exposing employees to multiple tasks helps managers see where employees could fit best in an operation. It allows us to identify the kind of work an employee feels passionate about so they are comfortable and more productive in the long term.
What kind of training is important for long-term employees, those who have been on the job for some time?
Voight: As swine genetics and management techniques evolve, it is a best practice to provide employees enhanced training that supports a more thorough understanding of farm protocols and how to reach animal performance potential.
Training can help employees and pigs thrive in all aspects of your operation. Supplement your employee training program for farrowing or wean-to-finish operations using materials available at pic.com/employee-training-resources.
PIC (Pig Improvement Company) is the global leader in swine genetics. PIC provides genetically superior breeding stock to pig producers and supports them with technical services to help them realize their genetic potential. PIC is a subsidiary of Genus, a UK-based company with a vision to pioneer animal genetic improvement to help nourish the world.
###
Document and hi-res images for download: https://bit.ly/3x5T1LC
[1] Boessen, C., Artz, G., Schultz, L. (2018) A Baseline Study of Labor Issues and Trends in U.S. Pork Production. Commissioned by the National Pork Producers Council. Updated in 2021 by Cook, H.