Extraordinary times call for performing ordinary practices with precision and purpose to maximize results. Producing a quality weaned pig is a good example. Ideally, every pig farrowed should have the opportunity to become a quality weaned pig, but it takes a combination of factors to make that happen. Although there is no standardized definition, three industry leaders recently shared the elements they feel are most important in achieving a quality weaned pig.
It’s more about quality than numbers, says Steve Dritz, DVM, Ph.D., global director of technical services at PIC. He says producers should keep three points in mind when it comes to quality: Know the characteristics that contribute to producing a quality weaned pig; understand what factors impact those characteristics; and acknowledge how important producing a quality weaned pig is to the success of each pork business.
Advantages
“We firmly believe that a good quality pig over a marginal or sub-par pig is always going to be more profitable, will reach market faster for less money, and is more likely to be a grade-A market pig in 5 months from weaning,” says Matt Davis, chief operating officer for Hord Family Farms in Bucyrus, Ohio.
Individual pig performance can lead to higher profit potential at market, says Dritz. “Also, populations with a higher percentage of quality weaned pigs are easier to manage post-weaning due to more predictable and consistent performance,” he adds.
Key Attributes
“A quality weaned pig possesses several key characteristics – not just one,” Dritz says. “These attributes are indicators for the nursery and grow-finish performance potential of the pig.”
Dritz says a quality weaned pig has the following attributes:
- Healthy
- Thrifty
- The right age/weight
- Consistency
He adds that thresholds for each characteristic are different for every flow, based upon the goals and constraints of each operation.
“It’s the interaction between these factors that add up to make a quality weaned pig,” explains Dritz.
Pig Health
Health is influenced by disease prevalence and circulation, colostrum quality and intake, robustness, genetics and gilt acclimatization protocols, Dritz says.
Davis describes a quality weaned pig as healthy and sound when it leaves the farrowing house and is ready to start eating upon entry into the nursery or wean-to-finish barn.
“If you want to have a healthy weaned pig, you have to have a healthy sow. You can’t have bad health in your sow herd and still produce a healthy pig,” he points out.
With 30,000 sows at Hord Family Farms, Davis knows how important it is to amplify the potential from every pig. In terms of vigor, Rodger Main, DVM, PhD, puts health status as No. 1, including the health of the sow and the source farm. He is director of the veterinary diagnostic lab at Iowa State University, where he also serves as a professor and faculty member.
“Both factors have a huge impact on the health of the weaned pig,” says Main.
“Also related to vigor is whether or not the animal wants to eat after it has been weaned – and that’s highly significant,” he adds.
Age and weight
Dritz says the combination of a pig’s age and weight is a critical attribute. “It’s not just one or the other,” he says. “t’s the combination of both the age and weight together that are key.”
“We know heavier pigs at a given wean age or at birth are usually better performing pigs,” he says.“ At PIC, the average pig litter size has increased,” Dritz adds. “Typically, that’s associated with less weight per pig born and in scientific literature there’s a strong correlation between the two. But PIC has been able to increase the piglet birth weight while at the same time increasing litter weight. That’s a good example of a swine genetic base that can help produce more quality weaned pigs.”
Davis says quality pigs are healthy, sound and have a good appetite. In other words, they are already off to a good start when they leave the farrowing house.
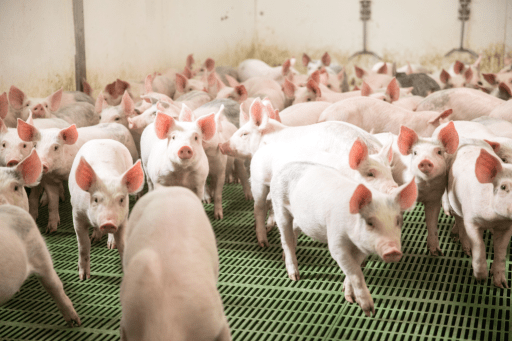
Along with heavier pigs at birth, research supports the benefits of a higher wean age in producing a quality weaned pig, starting with the classic work Main led nearly two decades ago. His PhD thesis focused on weaning age, which correlated with a heavier pig and faster growth rate to market.
“We found the impact of age at weaning when everything else was held constant was extraordinarily predictable and very linear,” he continues. “The studies were done in large commercial facilities, so that helped with replication.”
“While the actual dollar figures [on cost of production] have changed since that time, the biology and the basic take-home message from this work remains as relevant today as it was in those days so many years ago,” he emphasizes.
The Full Monty
As the three leaders point out, many factors come together to make a quality weaned pig. If just one component is missing, it can impact the others. It’s this emphasis on doing “everything that is necessary, appropriate or possible” – in other words, the Full Monty, to quote a British slang phrase – to produce a quality weaned pig. Producers who are willing to maximize their quest to produce a quality weaned pig will be more likely to reap the benefits in productivity and profitability.
Producing a quality weaned pig starts with having good people in the sow units who produce and raise the pigs and get them to weaning. “We truly believe it starts with the people,” Davis says. “If you have the best pig health, the best genetics and the best nutrition, but you’re lacking on people, your pigs are not going to be as good as if you have all of those things. If just one factor is missing, you’re going to feel it. They’re all very important.”
Article by JoAnn Alumbaugh, and originally featured in Farm Journal’s PORK
Are you looking for more information to support more quality weaned pigs? Try The Squeal Podcast #92, Quality Weaned Pig Part 3: Management, Husbandry Practices and General Health Issues.