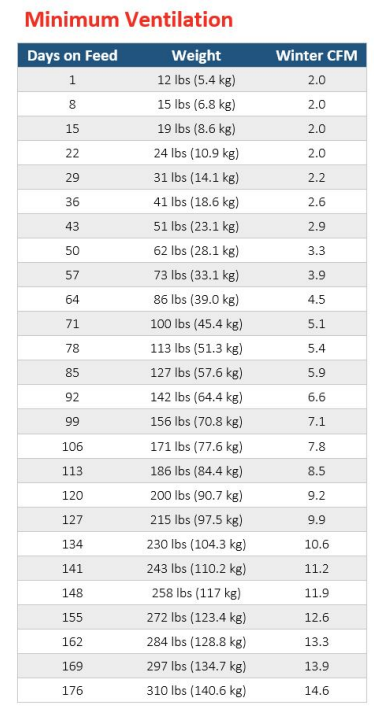
Optimizing ventilation is a matter of accurately setting up fans and inlets to maintain ventilation levels that meet the needs of your pigs.
However, to set up those fans and inlets properly, your targets for minimum CFM (cubic feet per minute) of air volume movement in the barn, must be accurate. Are you doing your calculations correctly? Check your math with PIC!
Minimum Ventilation (MinV)
Minimum Ventilation (MinV) calculations will be discussed below. It is important to note that systems should be set-up to never drop below these air exchange rates. These are the absolute minimum. MinV CFM recommendations are based on the minimum amount of air that should be exchanged to control humidity and gases. As barns warm up during the summer months or as pigs grow, our goals shift from ventilating to control gases and humidity to removing hot air for temperature control.
However, our ventilation systems should operate in minimum ventilation anytime room temperatures are below or within the first bandwidth set point (1.0-2.0°F, depending on season).
First, we must remember that MinV CFM rates increase as pig weights increase.
Using the table, let’s check calculations of CFM for a barn in the winter containing 1,250 weaning pigs, each weighing 12 lbs/5.45 kg. The chart indicates a MinV winter CFM for pigs that size of 2 CFM.
1,250 pigs X 2 CFM/pig = 2,500 CFM during minimum ventilation
For 1,250 market pigs of 300lbs/136kg, minimum CFM is 1,250 pigs X 14 CFM = 17,000 CFM. The above calculations in the minimum ventilation chart help us define our Pig Needs
Fan speed
For the same two size scenarios, let’s assume the barn has two sets of three 18-inch fans with a maximum fan capacity each of 3,600 CFM. Total barn fan capacity is therefore 21,600 in two sets of 10,800 CFM: 2 X (3 X 3600 CFM) (see diagram below).
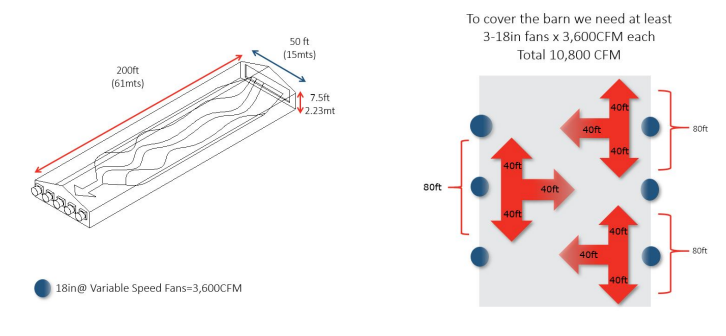
When determining which fans to operate, it is important to note that fans have different coverage area, therefore use your air speed meter (anemometer) to verify the fan is capable of extracting desired air from the furthest inlet.
From our calculations above, we know that 1,250 weaning pigs have a minimum ventilation need of 2,500 CFM. We divide our requirement by total capacity to get our fan speed:
2,500 CFM Required
10,800 CFM total fan capacity = requires fans to work at 23% of their capacity
For 1,250 market pigs that require 17,000 CFM, three fans won’t have enough capacity to achieve their minimum ventilation needs (as three fans will only provide 10,800 CFM). Therefore, we need to work with a second set of three fans, so let’s use six fans for this example:
- Six (6) fans provide 21,600 CFM at maximum
- To achieve 17,000 CFM, we need to work at 79% fan capacity (17,000/21,600)
Fan setting on controller
For the same two scenarios, let’s look at fan settings at the controller. Please use the following graph for reference:
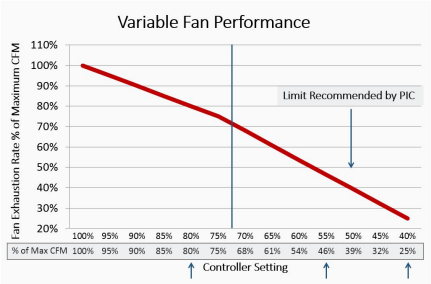
It is important to note that once fan settings drop below 75% at the controller, an increasing amount of fan efficiency is lost. Example: 50% at the controller = 39% real extraction rate From our calculations above, for weaned pigs, we need fans at 23% extraction rate. However, PIC does not recommend operating fans at less than 50% at the controller.
For market pigs, fans should run at 79%. That’s a speed of 79-80% at the controller. Fan exhaustion rate should always be reviewed by your supplier, we are only showing reference numbers here.
Inlet openings
Above, we defined pig needs and determined fan settings to match those needs. The final step in the process is setting the inlet opening correctly to achieve the desired air speed (std. 600 to 800 FPM) from each inlet to assure good coverage and ideal mixing of fresh air as stale air is extracted.
Additional references
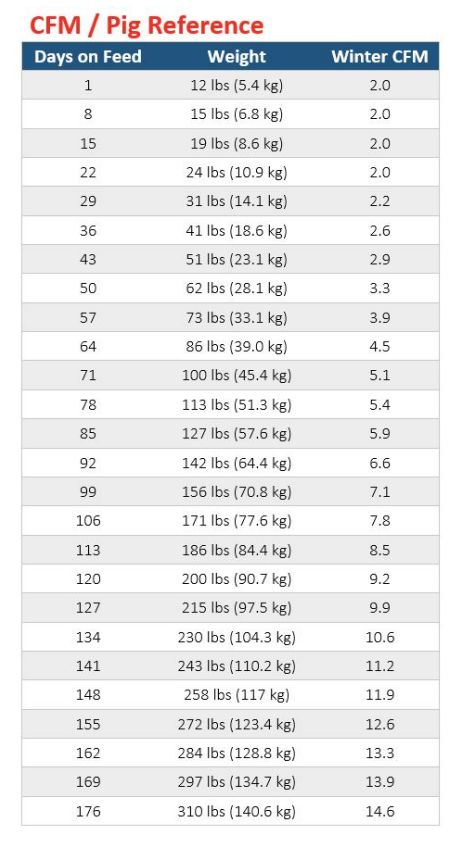
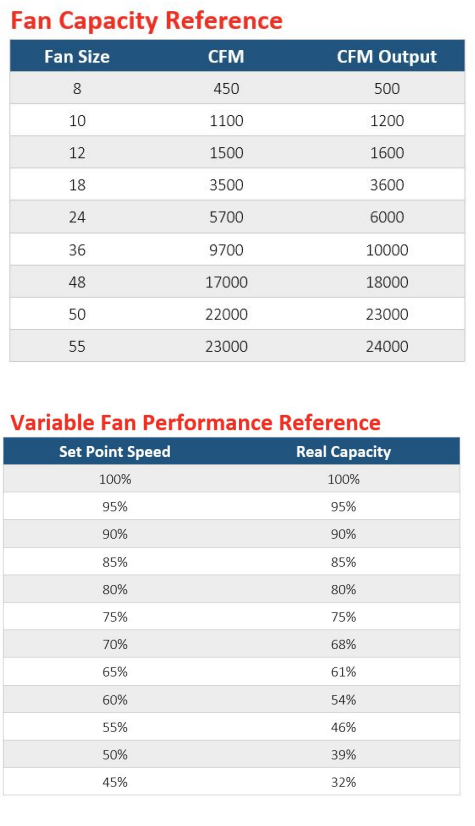